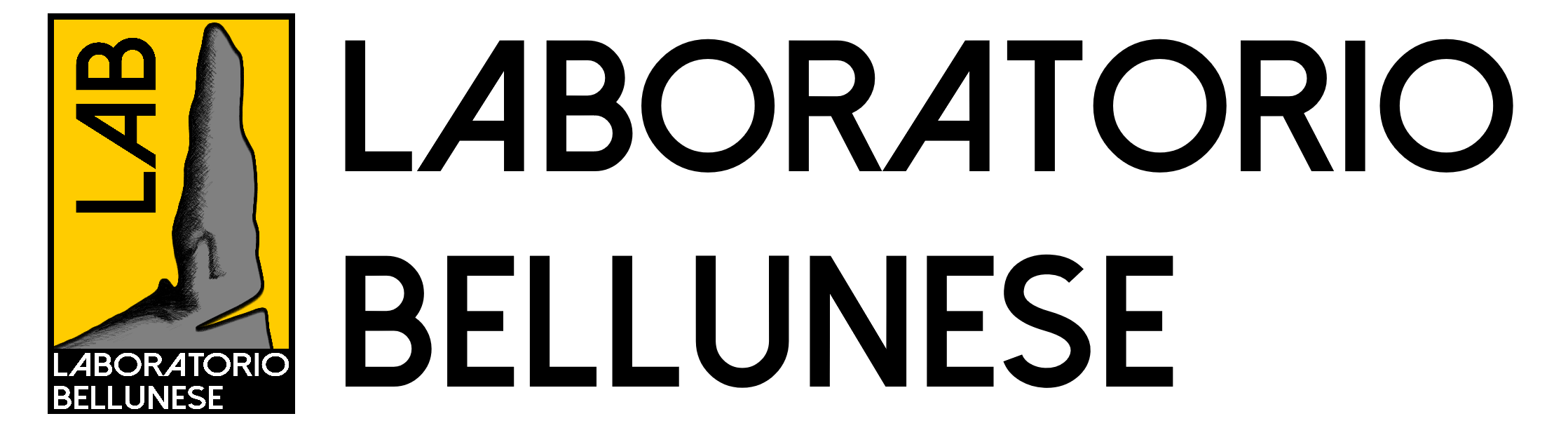
Con l’acronimo CUI si identifica ogni forma di corrosione che si venga a manifestare sulla superficie esterna di componenti coibentati. La CUI è un tipo di corrosione particolarmente insidioso in quanto si può sviluppare in superfici non accessibili e non controllabili visivamente. La CUI può essere causata da vari fattori e interessare indifferentemente impianti funzionanti a bassa, alta o a temperatura ambiente. Fluttuazioni di temperatura durante l’esercizio, o un esercizio discontinuo dell’impianto, aumentano notevolmente il rischio in quanto possono promuovere la formazione di condensa nel materiale isolante o sull’interfaccia isolante/metallo.
Bisogna tenere ben presente che affinché la CUI si manifesti occorrono tre elementi: metallo, aria (ossigeno) e acqua (elettrolita). Nella CUI l’acqua deriva da fenomeni di condensazione oppure può filtrare dall’esterno.
La CUI può manifestarsi in forme diverse a seconda delle combinazioni di metalli ed elettroliti che possono venire a formarsi. Le principali sono le seguenti tre:
- Corrosione galvanica: quando la CUI è determinata dalla presenza di un elettrolita (acqua e ioni) nell’interfaccia metallo/isolante che permette il passaggio di un flusso di corrente fra metalli dissimili;
- Corrosione acalina o acida: CUI che si manifesta in seguito alla penetrazione di acqua ed alla conseguente formazione di un ambiente acido o basico all’interfaccia del metallo coibentato;
- Corrosione da cloruri: CUI determinata dall’ingresso di acqua e della presenza di cloruri solubili all’interno del materiale isolante. I cloruri accelerano la velocità di corrosione, ma nel caso in cui il metallo coibentato sia un acciaio inossidabile possono portare ad insidiosi fenomeni di corrosione localizzata per pitting, o, nel caso l’acciaio sia austenitico e le condizioni lo permettano, a tensocorrosione (ECSCC).
La CUI è un problema noto, molto studiato ed anche affrontato dal mondo normativo (API 510, API 570, API RP 574, API RP 583). L’oil&gas ed il settore chimico lo conoscono molto bene ed esso rappresenta uno dei principali costi di manutenzione per il piping (40/60%).